Sponsored article
What does the die cutting process involve?
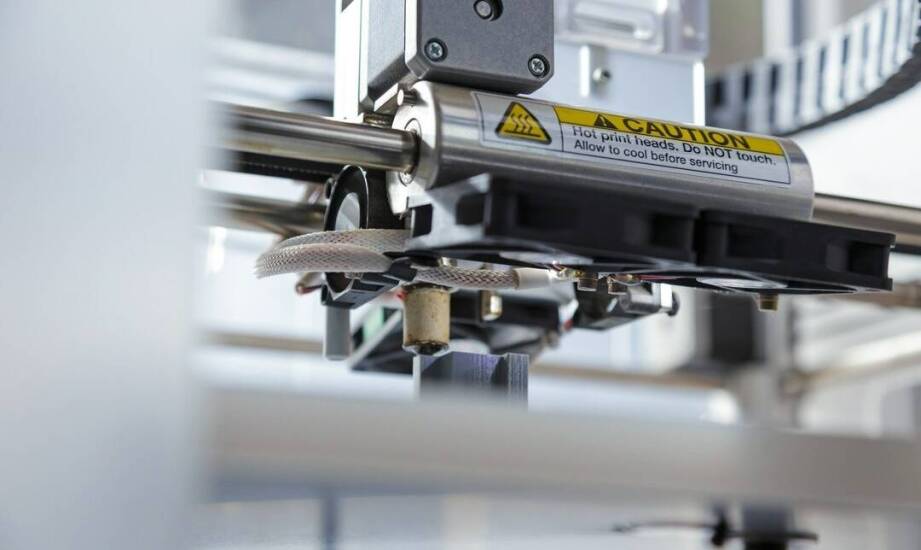
Die cutting is a material processing method involving the precise cutting of shapes or holes from a variety of raw materials. This process is carried out using specialised equipment, such as die cutter machines, which ensure high efficiency and accuracy. With this technology, materials of varying thicknesses and hardness can be easily processed, making die cutting indispensable in many industries.
How does die cutting work?
The basis of the die cutting process is the tools consisting of a die and a punch. Depending on the device used, the material is pressed against the die using rollers or a punch to achieve the desired shape. An example of technology in this area is roller die cutter machines, which are distinguished by their ability to precisely cut materials of different thicknesses – from thin films to thick cardboard and technical foam.
The high pressing force, up to 150 tonnes, allows raw materials such as PVC, PET, HDPE, natural and synthetic leather or technical fabrics to be processed. Thanks to modern solutions, such as polymer-coated rollers, the die cutting process runs smoothly and tool wear is significantly reduced.
Use of die cutter machines
Die cutting is used in a wide range of industries, from the manufacture of packaging to the cutting out of technical components. Roller die cutter machines are ideal for:
-
cutting corrugated and fibre board,
-
production of blisters and other packaging,
-
processing of thermoformable films,
-
precise cutting of foam and composite materials,
-
cutting leather and textiles.
With the option of automatic and manual modes, the machines are extremely versatile and can be adapted to the needs of different production lines.
Why bet on precision?
Precision die cutting not only guarantees repeatable shapes, but also saves time and materials. Machines equipped with PLC control systems enable quick die changes and flexible adaptation of operating parameters to specific tasks. This solution is ideal for both short production batches and large orders.
Zemat Technology Group’s range of advanced die cutter machines meets international ISO and CE quality standards. As a result, users can count on reliability, safety and low operating costs.
Benefits of modern die cutter machines
-
Efficiency and economy: Roller machines have a capacity of 20-30 cycles per minute.
-
Versatility: Capable of working with materials up to 13 mm thick and quick tool changes.
-
Comfort of use: Intuitive control requires no specialist qualifications.
Modern die cutting technologies allow companies in various industries to increase their productivity and deliver the highest quality products. Choosing the right equipment is an investment in precision, efficiency and competitiveness in the market.